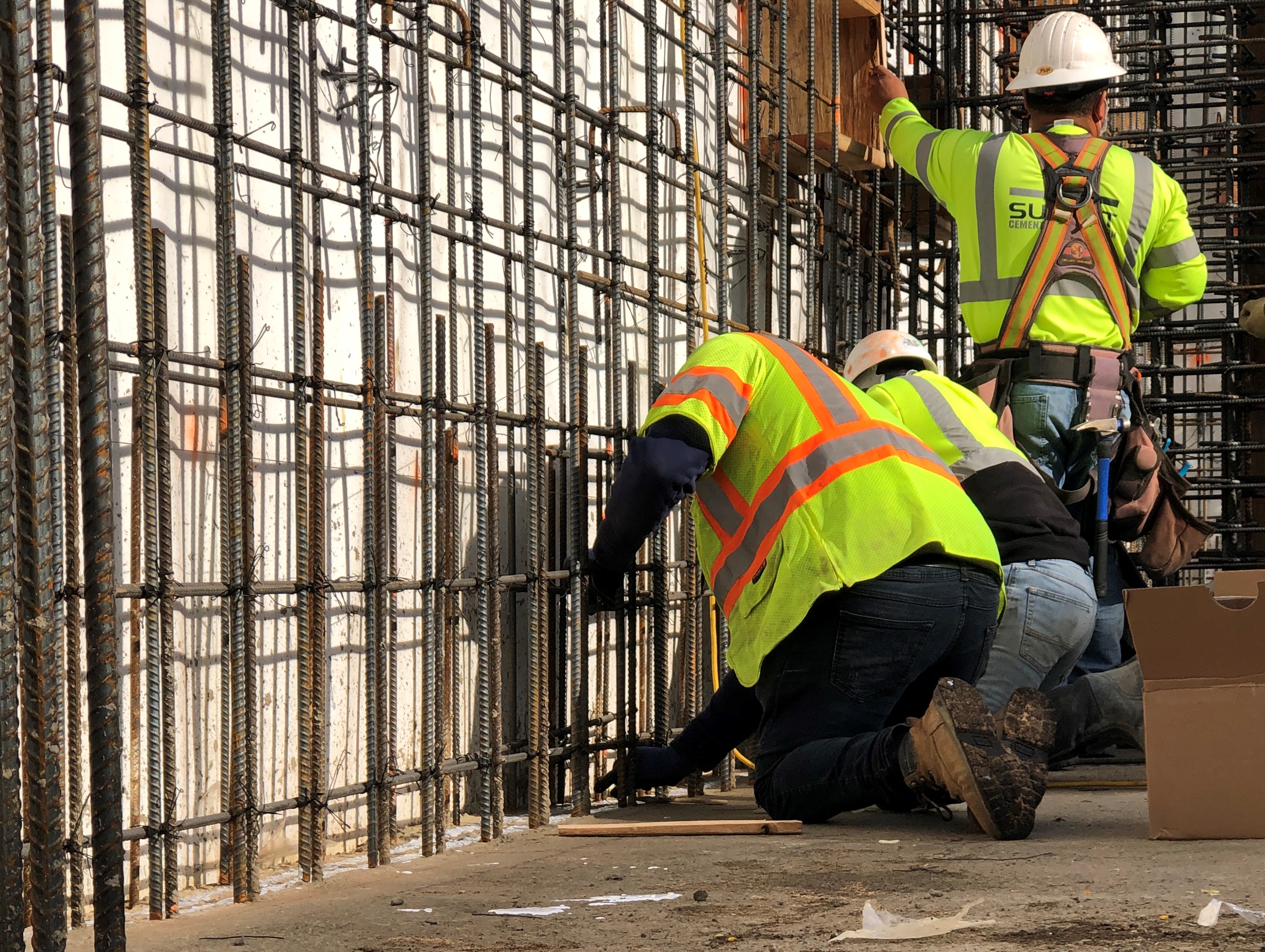
Roystone Apartments, developed by Vibrant Cities, is an eight-story mixed-use apartment building in the rapidly developing Uptown neighborhood of Seattle’s lower Queen Anne. The building will include roof decks and ample amenities for residents to enjoy.
The Roystone Apartments (74,096 sq ft) will have 93 units with ground-floor retail and a one-story below-grade parking garage. The site has a unique history: A Texaco gas station operated on the land from 1923 to 1993. In 1986, the Washington Department of Ecology responded to complaints of gasoline odors at the adjacent apartment complex. An investigation conducted from 1986 to 1990 revealed the former gas station to be the source.
“Many dense urban locations struggle with the dirty legacy left behind by the corner gas station,” explains Principal Robin Murphy, Jackson Main Architects, the firm responsible for the project design. “Failed antiquated underground storage tanks (UST), some originally buried as far back as the 1920s and 30s, leak diesel and gasoline into adjacent soils causing an underground plume of contaminated soil and groundwater. With rising demand for more urban residential development, effective contaminant mitigation methods must be employed to repurpose these properties.”
Two wells were installed to remove petroleum from groundwater, and seven underground storage tanks were removed and a soil vapor extraction and groundwater recovery system put in place. Texaco’s successor, Chevron Environmental Management Company (CEMC), upgraded and operated the system from 2003 to 2008 under Ecology’s Voluntary Cleanup Program.
Pavilion Construction, Roystone’s general contractor, began further site cleanup in March 2020. In addition to the seven USTs already removed from the site, an additional three USTs containing diesel and waste oil were removed.
Pavilion’s site superintendent, Roger Woods, explains, “In total, approximately 16,235 tons of petroleum-contaminated soil, 62 tons of soil containing solvents, and 1.47 tons of soil containing waste oil were removed and disposed off property. Site logistics and careful planning were essential for the proper execution of these site contaminant clean-up efforts. All soil containing concentrations of contaminants above allowable MTCA soil cleanup levels have been removed from within the Property boundaries.”
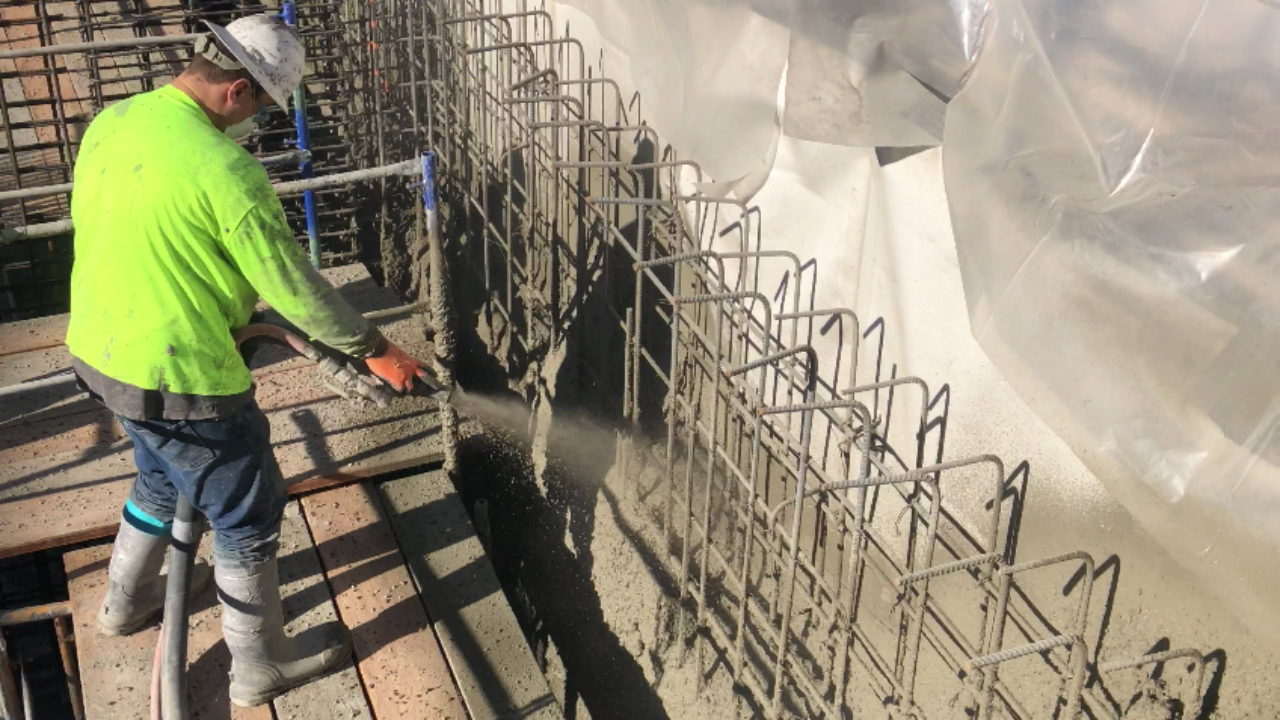
Considering that the site also experiences shallow groundwater, the BEE Consulting project design team was tasked with the selection of an appropriate waterproofing and contaminant vapor intrusion system.
EPRO’s PreTak membrane was installed at all underslab locations directly over compacted fill and vertically against the soldier pile lagging support of excavation (blindside waterproofing). The blindside assembly consisted of EPRO’s e.drain drainage composite with embedded filter fabric against soldier pile lagging with PreTak mechanically fastened to the lagging.
Sheet metal field fabricated “box outs” detailed with PreTak membrane were installed over all tie-backs. To accommodate the use of structural shotcrete for the below-grade foundation walls, all seams were reinforced with an additional application of four-inch wide PreTak PreTape. After concrete is applied to the surface of PreTak, PreTak’s specially formulated, pressure-sensitive adhesive integrally adheres the surface of the membrane to the fresh concrete with over 20 pounds per inch of adhesive bond strength.
This fully adhered waterproofing and contaminant vapor intrusion barrier system effectively eliminates the potential for lateral water migration between the installed membrane and concrete substrate while effectively protecting the structure from residual subsurface contamination.
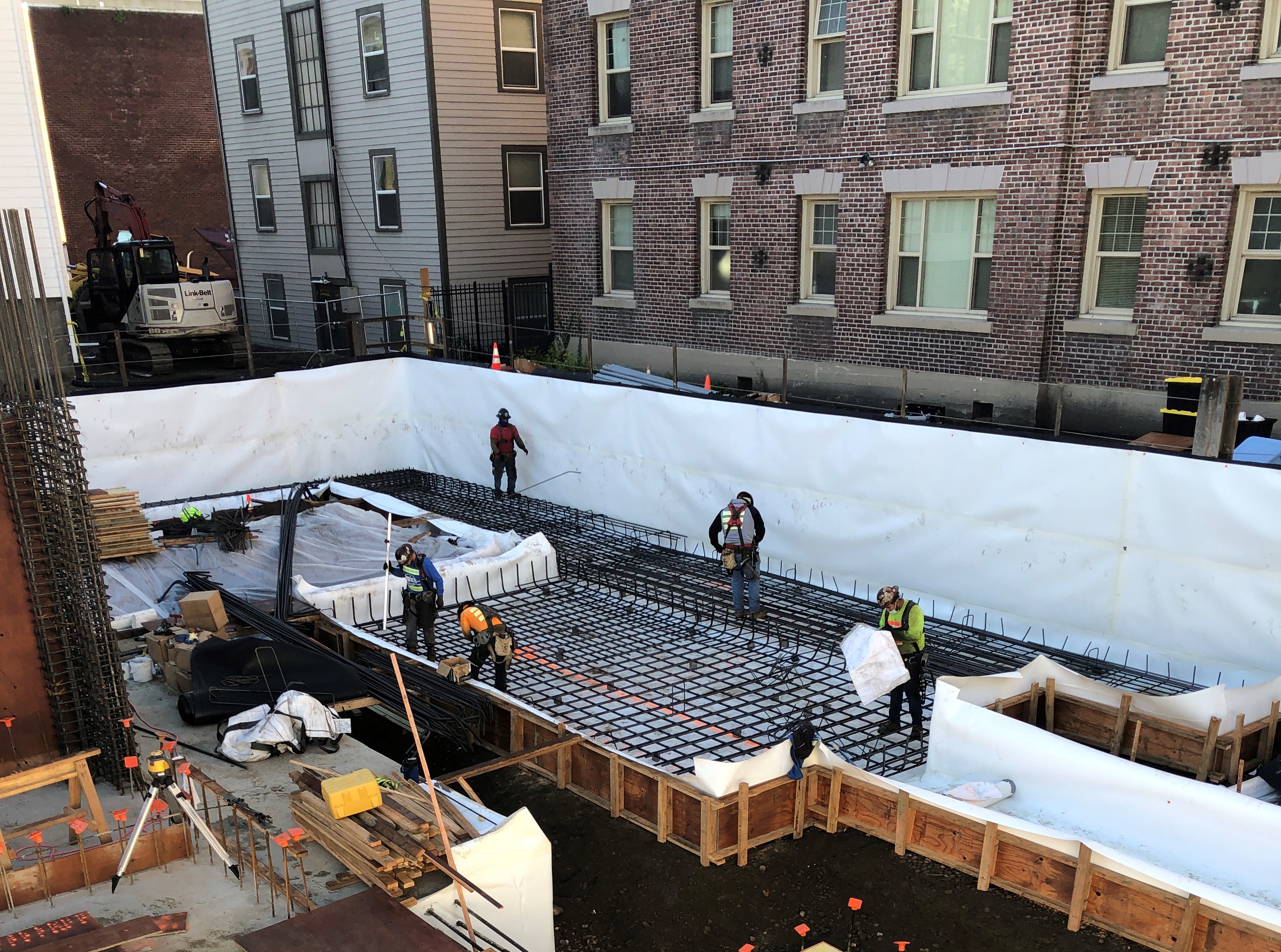
Project experience with PreTak has been positive. “Not only was PreTak a solid performance choice for this project, but it was also the most cost-competitive option that we evaluated. EPRO’s approved applicator Emerald City Waterproofing was able to provide cost savings to a competing bidder with a system claiming similar performance.” Pavillion’s superintendent Roger Woods explains. “Additionally, EPRO’s onsite technical assistance has been instrumental in helping solve the inevitable site challenges as we have progressed on this project.”
PreTak is a pre-applied vertical and horizontal high-density polyethylene (HDPE) sheet waterproofing membrane combined with a pressure sensitive adhesive that mechanically bonds to cast in place concrete and shotcrete in both blindside shoring and under slab applications. This entire below-grade building envelope solution provided an effective waterproofing and contaminant vapor barrier membrane necessary to rewrite the legacy of this Seattle corner gas station to serve the community safely, effectively and economically.
If you want to learn more about PreTak, click here. To read more about EPRO’s involvement in other projects, take a look at our other case studies, including how we helped a multi-use redevelopment project in DC, a waterproofing success story in LA and created a deck waterproofing solution for a resort in Las Vegas.