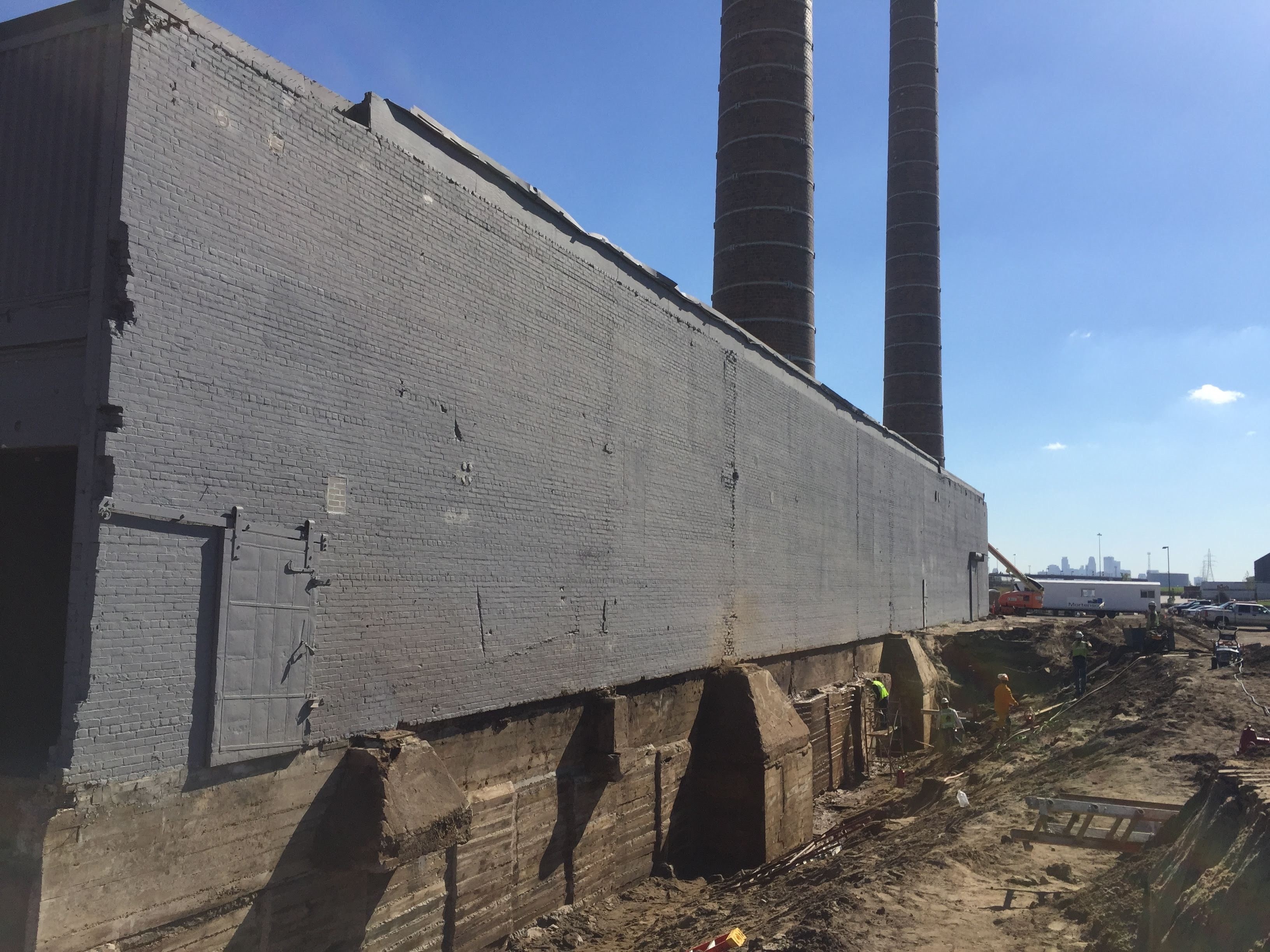
Few things can quickly destroy the value of a property like water infiltration through the building foundation. Water is one of the biggest threats to the retention value of a structure. Proper waterproofing with the correct materials is essential.
What can be done if a structure was improperly waterproofed or, in some instances, not waterproofed at all? Restoration waterproofing is then required. Oftentimes, restoration waterproofing becomes a necessity due to interior water intrusion or if interior space is repurposed and a more watertight interior finished space is required.
Restoration waterproofing presents unique challenges for applicators, designers and building owners that are distinct from new construction waterproofing. As-built drawings may be unavailable or original project drawings incomplete. The foundation waterproofing may be unknown until excavation. Older waterproofing materials may contain asbestos or coal tar pitch. These materials are now known to be harmful and may require expensive abatement.
Most projects are bid before excavation. Typically, it is not possible to truly understand the scope of work necessary until excavation and preparation of the foundation are completed, which can be the most time-consuming and costly portion of restoration waterproofing.
This means that restoration applicators must bid on the project with incomplete information, mostly concerning existing waterproofing and substrate conditions. Uncertainty always increases costs.
Designers must consider material tie-ins and system compatibility for transitions to at-grade flashing or existing waterproofing that may remain in place. Building owners must consider potential schedule or budget overruns due to unforeseen circumstances related to exposure of the foundation.
The Project
Originally constructed in 1929 to house the boiler room for a manufacturer of firefighting water pumps, the Northern Stacks structure was repurposed during World War II to produce ship guns for the U.S. Navy.
The production facility was awarded six stars for Excellence in Production, one of only eight production facilities nationwide throughout World War II that received such accolades and only one of two left standing today. Fulfilling a new purpose, this structure was restored and is now home to the Forgotten Star Brewing Company.
The Problem and the Solution
To repurpose this structure, the infilled inside floor was excavated in sections to recreate below-grade space. The original foundation was poured in place against lagging without waterproofing. Due to the presence of the Mississippi river nearby and water table conditions above the footing level, it was necessary to apply waterproofing to the structural walls to properly protect the below-grade space from water intrusion.