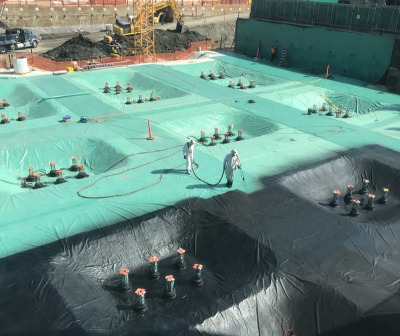
The building envelope protects interior building systems and occupants from the elements, including heat, cold, wind and, in particular, water. Water infiltration is one of the most pervasive and difficult to control issues for any building owner or operator. If you’ve dealt with water damage, we feel your pain. If you haven’t, then you’re unusually lucky, and we’d like to know your next Power Ball numbers.
Water damage can lead to mold growth, indoor air quality issues, foundation cracks and more. Many internal and external building materials may prematurely fail, and other concrete building envelope elements may be compromised.
New build or renovation aside, the singular best way to protect your building is to choose the right waterproofing materials during the initial design phase. Waterproofing systems can protect against wet weather conditions or groundwater, keeping occupants safe from contaminated groundwater or otherwise.
What to Consider when Specifying Waterproofing Materials
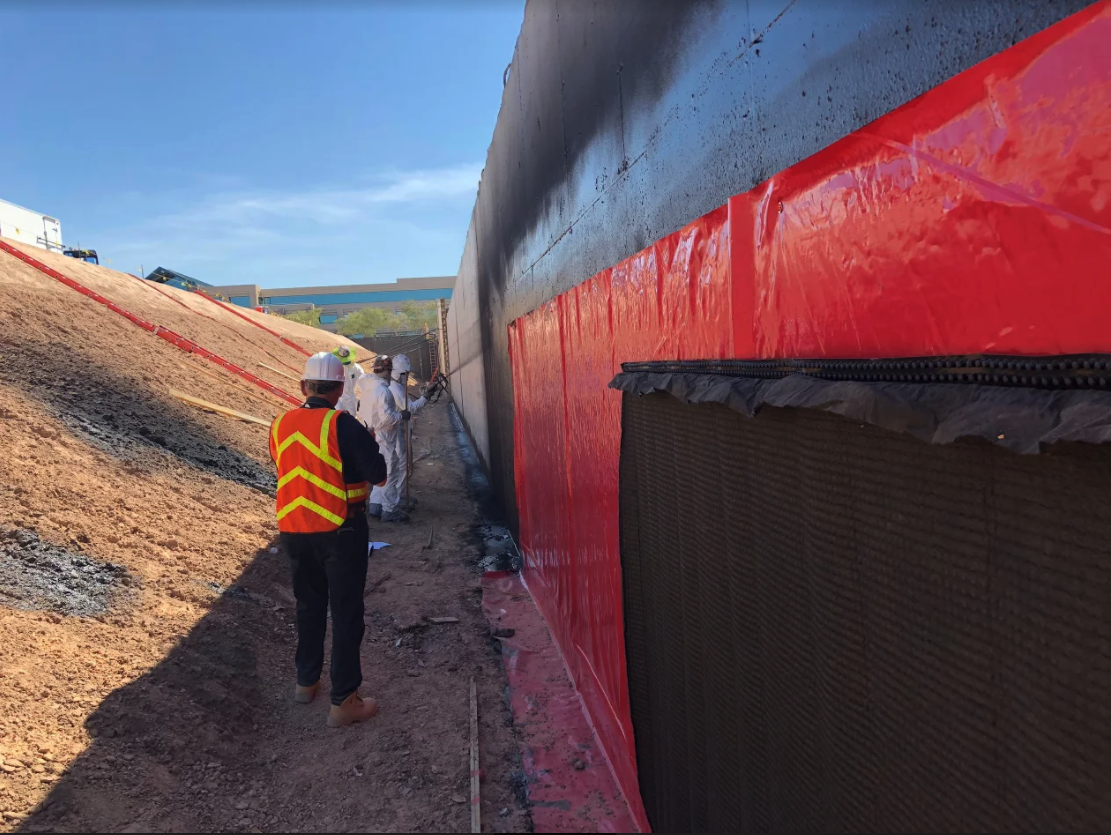
High-quality waterproofing materials will have several features in common. Look for those that differentiate themselves by offering:
- As few seams as possible: The seam is the weakest point and most likely to fail over time or through repeated exposure to water.
- Full adhesion to the substrate: Water always chooses the path of least resistance. Make sure your waterproofing material does not allow for pockets of air or bubbling to form between the membrane and substrate.
- Look for composite systems: Layers of different waterproofing membranes will help the whole system to last longer and let you address issues before they become critical problems.
- Efficient installation: No matter the building type, time is money in construction. Choose a waterproofing material that can be installed quickly and efficiently without compromising quality and creating delays.
Choosing the Right, Project-Specific Waterproofing Materials
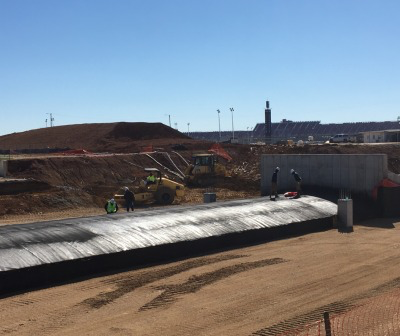
Once you’re confident you have chosen a high-quality, high-performing waterproofing solution, the next step is to select the product that will work for your specific needs.
Factors to consider include:
- Whether your project is above-grade or below-grade
- The overall area of the space that needs waterproofing
- Slope and drainage included in the design
- The presence of contaminants in the water
- Desired durability and the necessary level of redundancy
If Your Project is Above-Grade
Above grade waterproofing is essential. A structure that has no flashings, no sealants and no membranes on the deck or balcony area won’t last more than a few years. Products used for above-grade waterproofing also differ substantially from their below-grade counterparts.
Above-grade waterproofing products must be watertight, adaptable to a range of temperatures, resistant to UV light, and in some cases aesthetically pleasing. Balconies, parking decks, rooftop terraces and plazas need waterproofing to protect the building envelope from moisture ingress.
That’s why builders feel confident with EPRO’s Deck Protection System. It guards against water infiltration on podium decks, green roofs, balconies, and planters. You can use EPRO’s e.Protect+ system for large projects with two layers of reinforced membrane. Or you can use EPRO’s e.Proformance system for small, lightweight projects.
If Your Project Is Below-Grade
Waterproofing below grade brings has a unique set of challenges. Concrete foundations may be under continual hydrostatic pressure even when groundwater is not present. In many areas, new construction sites are situated on brownfields or repurposed industrial properties. Here, issues like contaminated groundwater mean contractors need to choose a product that also mitigates vapor intrusion by keeping out solvents and other organic chemicals along with water.
For example on this construction site, contractors and project managers needed a below-grade waterproofing membrane to meet their site condition requirements. The office building was built on a contaminated wetlands area in Playa Vista, CA. Contractors working with waterproofing and environmental experts chose EPRO’s below-grade E.Protect+ System composite waterproofing system. This system keeps groundwater, methane gas and organic solvents out of the building, and it is designed to adhere to the concrete quickly and will not sink or settle as the surrounding soil subsides over time.
If Your Project Is Smaller
Smaller area projects like a balcony or large planters may only need limited waterproofing. While all concrete is porous, these areas are less likely to be exposed to significant standing water, hydrostatic pressure or traffic, so a lighter waterproofing product may be sufficient.
A concrete waterproofing product like EPRO’s above grade E.Proformance Deck Protection System is designed with smaller spaces in mind. It offers 70 mils in three layers of composite protection that can be installed over concrete topping slabs, plywood substrates and highly sloped decks.
A thinner, lighter waterproofing membrane can be installed quickly and provides necessary protection when installed in areas that drain quickly and where standing water isn’t an issue.
If You Need Durable Protection Over a Large Space
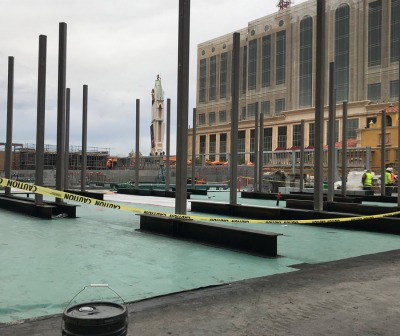
According to Angie’s List, the cost of fixing flood damage to a basement can range from $10,000 to $50,000 for a residential space and significantly more for a larger commercial space depending on the amount of water and extent of the damage. The larger the space, the larger the risk, which is why investing up front with a high quality waterproofing system is so important.
For example, The Venetian is a global attraction, primarily because of its rooftop pool. It spans two acres and is considered to be somewhat of a structural wonder. During a recent renovation, the entire pool deck was resealed, requiring contractors to expose and strip away more than three acres of the old waterproofing.
Vegas winters can be windy and lead to an excess of dust and debris on construction sites. In situations like this, contractors could benefit from a concrete waterproofing product that applies quickly and adheres fully to the substrate to prevent the potential for damage once the pools are filled and operational again.
For the Venetian project, EPRO’s E.Protect+ was selected. It provides 136 mils of protection in three redundant layers, helping to ensure the system’s integrity, even with the adverse wind and dusty conditions.
If You Need to Waterproof Quickly
Efficiency is critical in any project, and waterproofing concrete as quickly as possible helps reduce the chance of water intrusion, even during construction.
At the Ritz Carlton in Paradise Valley, AZ, the 200-room hotel surrounded by villas and single-family homes needed two below-grade parking garages. However, the waterproofing product selected initially wasn’t available. For such a high-profile project, delays could be damaging.
To keep the project on track, the general contractor selected EPRO E.Protect e.spray to add an 80 mil waterproofing barrier. This product can be applied to even green uncured concrete, which kept the project on schedule and accelerated the timelines.
Which Waterproofing Product Is Right for You?
With warranted waterproofing and contaminant barrier systems for below-grade applications, including shoring walls, walls, underslabs, and above grade deck applications, EPRO is the #1, single-source provider for your entire project.
EPRO offers a “good - better - best” system for each application, which allows customization and flexibility to perfectly match an EPRO system to your project based on budget, site condition, construction materials, timeline and desired level of protection.
Choosing the best waterproof building materials will be critical to any project’s success and the building’s longevity. If you need help selecting a quality waterproof product, or collaborate on an upcoming project, contact the experts at EPRO.