Elevator pits are typically the deepest part of building construction, extending a minimum of five feet below the lowest floor slab, below the capillary break drainage layer of the mat slab. At this depth there is an increased likelihood of perched water or ground water, hence the need for robust waterproofing.
There are state-specific requirements for elevator pits, some more stringent than others. In California, for example, the state requires inspections every two years and if any water is found in the pit, it will not pass.
Elevator Pit Design and Waterproofing
There are multiple elevator pit designs, and the best avoid structural elements, such as grade beams, footings, etc:
A standalone pit is the least complicated design and typically preferred because it does not interfere with mat slab structural elements. The waterproofing wraps the entire pit creating a continuous envelope.
An elevator pit with integrated grade beams has more challenging detailing; the waterproofing cannot wrap the entire pit as easily due to the location of the beams. There is no hard and fast rule regarding where the waterproofing needs to terminate or extend, so there is often confusion about how much waterproofing to apply.
An elevator pit embedded into the mat slab. This is the most critical and vulnerable part of the structure. In this scenario, it would be ideal for the waterproofing to run continuously under the slab, including under the elevator depression for maximum protection against water ingress. However, this is not typical in slab-on-grade applications – challenges include placement of waterproofing, and when and how it is terminated.
In addition, reduced mat slab thickness at base of elevator pit can be susceptible to cracking, exacerbating the potential for leakage.
Elevator Pit Waterproofing Materials
Elevator pit waterproofing often combines both pre-applied and post-applied products because of the way pits are constructed. Bentonite is frequently used for it is quick and easy application. Self-adhered waterproofing, like PreTak, is another common material, and peel and stick self-adhered sheet membrane waterproofing is also preferred due to its ease of application.
Integral waterproofing, which is a special concrete admixture, is also a popular option. When the concrete is hydrated, a chemical reaction occurs to create acrystalline structure which grows to block the pores within the concrete. It can be quite susceptible to cracking and some consider it to be the lowest level of waterproofing.
Elevator Pit Waterproofing Challenges
Water and poor design and detailing are the top two challenges associated with elevator pit waterproofing. If the pit is not properly dewatered or if there is an open seam in the waterproofing, water can collect under the waterproofing and – quite literally! - create a waterbed. The membrane is then floated. Any water must then be removed via sump pump. In extreme cases, the membrane has to be cut before water is removed – and of course this is less than ideal!
With improper design and detailing, any waterproofing system will be weakest at transitions or penetrations. Different materials can, however, combine to ensure that all potential points of water ingress are well protected.
The following are EPRO systems for waterproofing elevator pits:
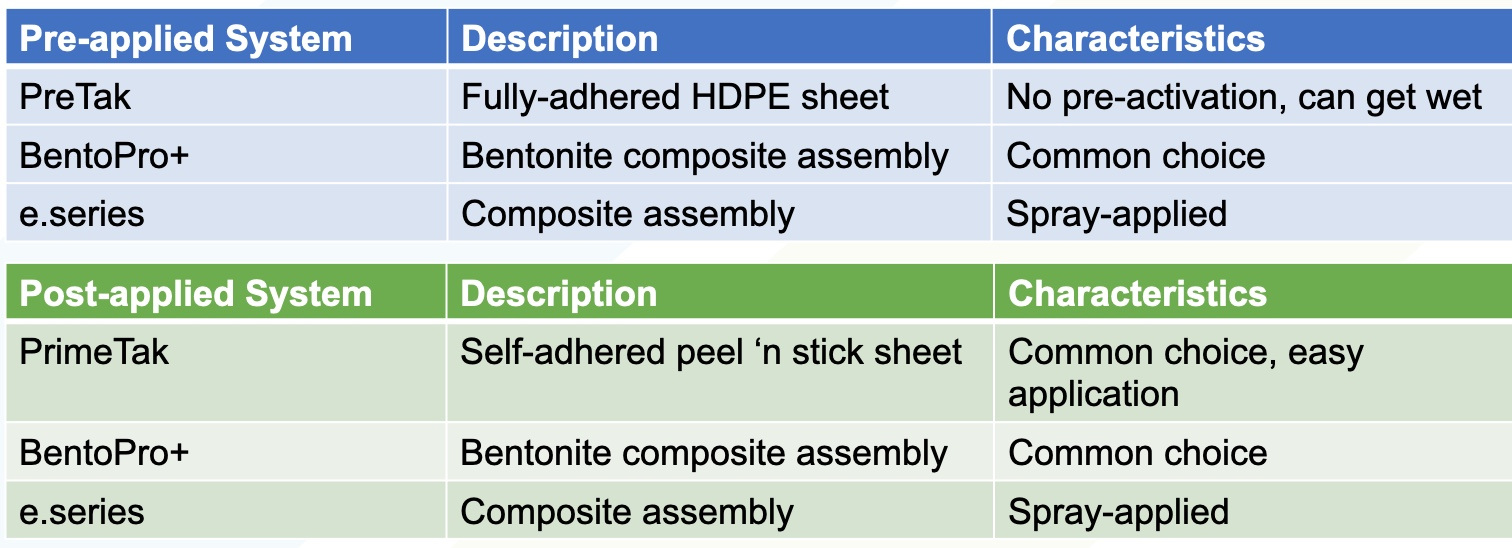
Our knowledgeable and experienced EPRO team are happy to be a resource for your elevator pit waterproofing needs – contact us to discuss your project and any specific elevator pit waterproofing requirements!