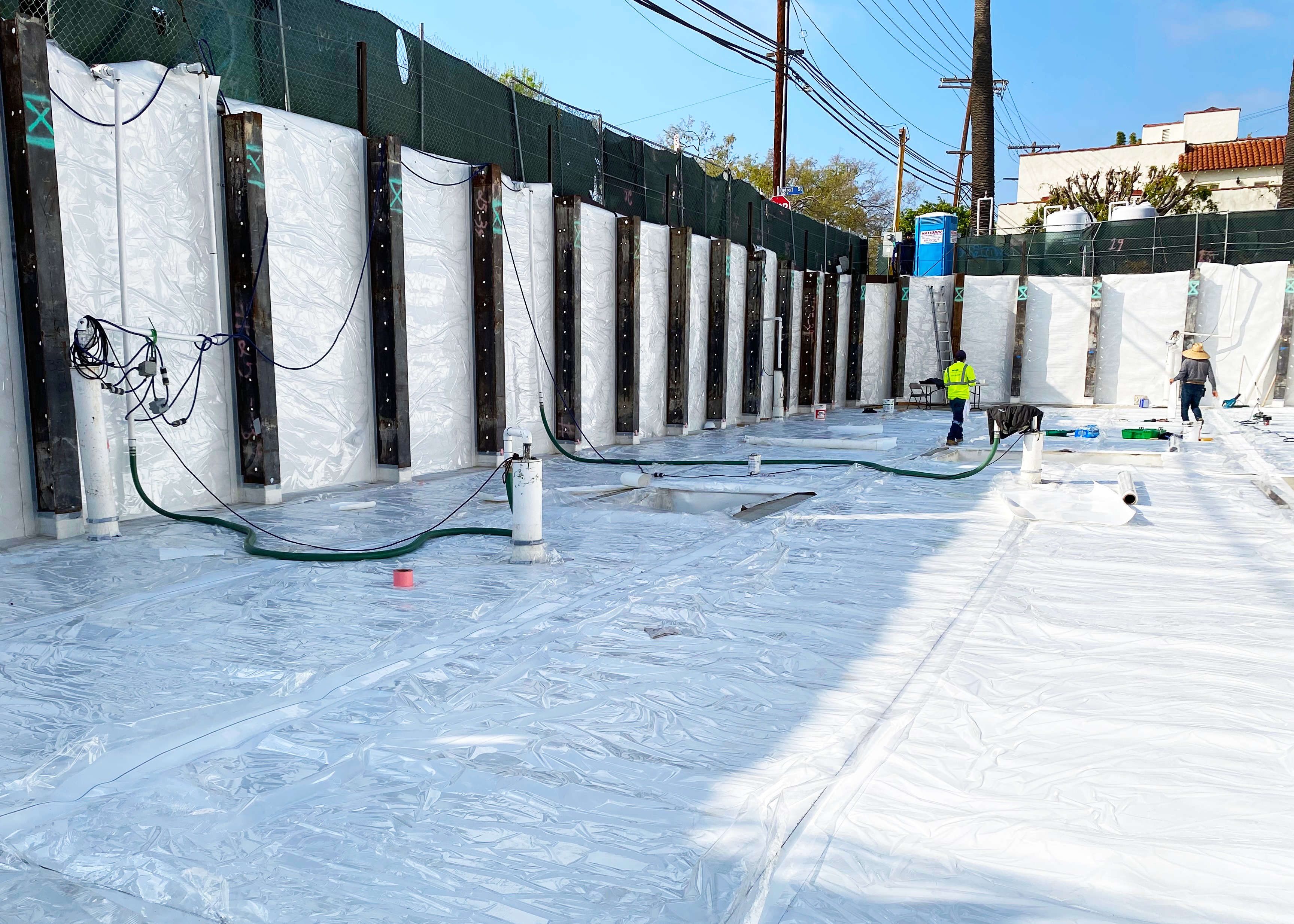
Choosing the right products to protect your building from water damage is an important part of building design. No matter the size of the project, a waterproofing membrane is the best way to prevent water infiltration.
With a variety of commercial waterproofing solutions available, it can be difficult to determine the best type of material for each project. Understanding how waterproofing systems fit into each project will help in choosing the right product that will protect your building, and save time and money.
Here are some quick tips for selecting the right waterproofing membrane.
Start By Consulting With a Professional
Before beginning any project, it’s always a good idea to speak with an experienced advisor who can help you better understand and evaluate project needs from a building materials perspective.
For example, EPRO's systems can be customized to fit specific site conditions. If you need help selecting a quality waterproofing product or want to collaborate on an upcoming project, contact the experts at EPRO for help matching the right EPRO system to your project based on budget, site conditions, construction materials, timeline, and desired level of protection.
Know the Building’s Construction
Without fail, water will always choose the path of least resistance, so you need a waterproofing system that has no weaknesses for water to exploit.
Here are some questions to ask about the building’s components and design that will help in choosing products. We’ll cover these questions in more detail throughout the rest of this article.
- Is the project in question above-grade or below-grade?
- What will the waterproofing be applied to?
- Is drainage included in the design?
- Will shotcrete be applied to the waterproofing?
- What are the desired durability and the necessary level of redundancy?
After identifying the conditions and where waterproofing needs to occur, the next step is to address the specific concerns about each site area.
Understand the Site Conditions
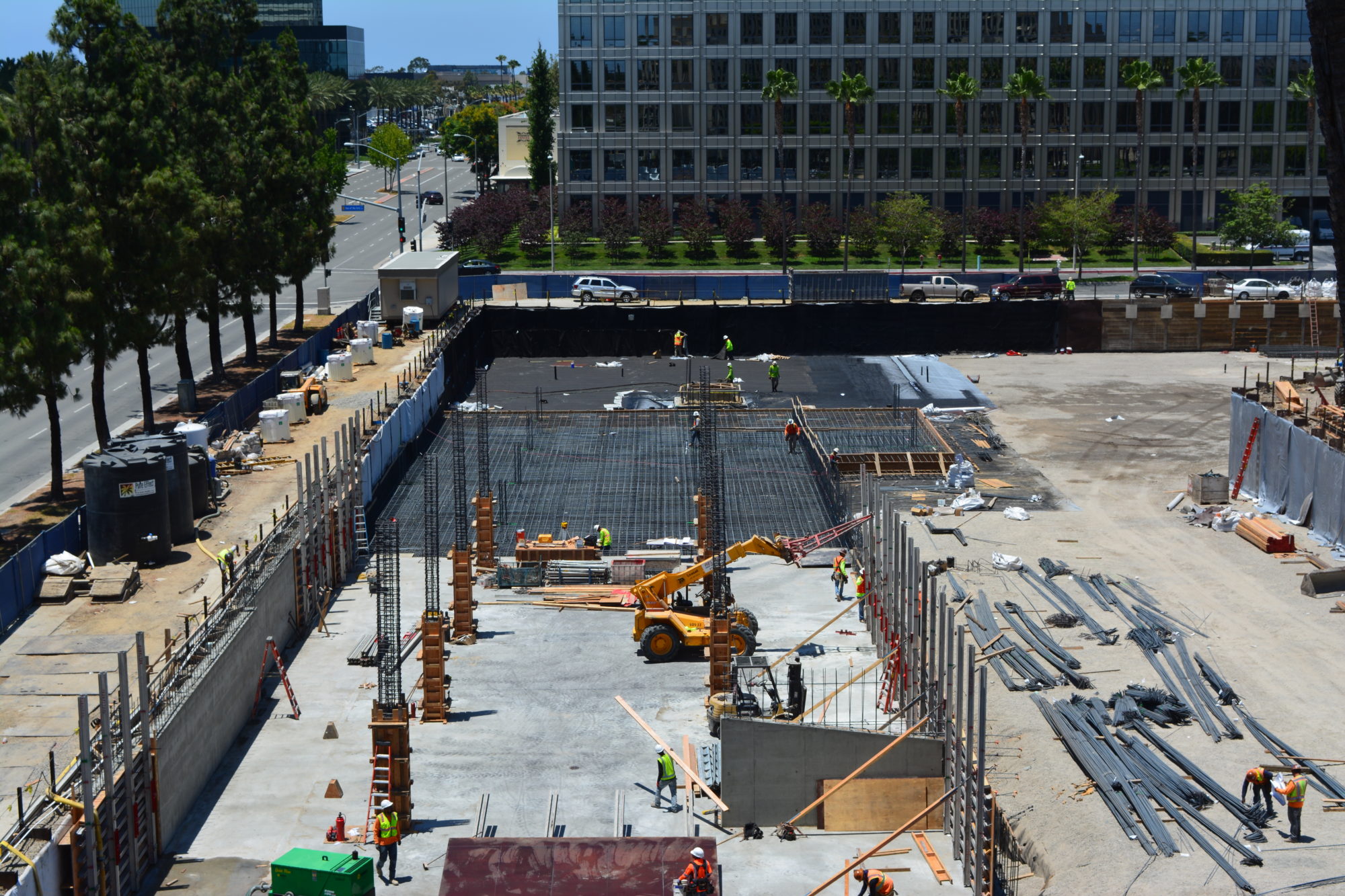
There are several crucial questions to ask about the job site as a whole before deciding on a final product. Each question will help narrow down the type of waterproofing membrane needed.
1. Are above-grade or below-grade materials needed — or both?
Knowing the basics for what is needed is a good starting point.
- Above-grade waterproofing products must be watertight, adaptable to a range of temperatures, resistant to UV light and, in some cases, aesthetically pleasing. Balconies, parking decks, rooftop terraces and plazas need waterproofing to protect the building envelope from moisture ingress.
- Below-grade waterproofing brings a unique set of challenges. Concrete foundations may be exposed to perched water or nuisance water pressure even when groundwater isn’t present. This causes water to collect in the looser soil, keeping it close to the foundation where it can potentially damage the foundation.
2. Has the water table been determined?
Always check to see if a geotechnical report has been conducted before choosing a waterproofing membrane. There are a few things to determine about the site including:
- Water Table Level: Where is the groundwater table and where is the highest elevation that the water table may be present?
- Presence of Hydrostatic Pressure: If the building foundation is being constructed at or in near proximity to the groundwater elevation, the building can be exposed to hydrostatic pressure.
3. Are there signs of contaminated soil vapor or gas?
Are there ground gases present at the job site? This can include radon, methane and carbon dioxide. It’s also important to realize that there may also be contaminated vapor that can permeate your waterproofing membrane.
A phase 1 or phase 2 environmental report will identify chemicals present in the soil or groundwater and will help to determine if your waterproofing needs a level of chemical or vapor intrusion protection.
Determine How the Building Construction Will Impact the Waterproofing
The following are considerations will help identify how the waterproofing will impact the work:
- Where is the waterproofing within the entire building schedule? Depending on the type of waterproofing to be completed, the membranes chosen can be applied throughout different phases of construction, and there may be extended periods of time between certain applications. Making certain the selected system can withstand the exposed duration times is important.
- How will the installation be impacted by other building trades? Waterproofing installation needs to be done correctly. Coordinating with the general contractor and other trades is critical to a successful installation.
- How do the site conditions and concrete/shotcrete placement impact the installation process? When installing pre-applied waterproofing, the use of cast-in-place concrete versus shotcrete can impact waterproofing system installation procedures because additional installation requirements may be needed for shotcrete, especially in hydrostatic conditions. Post-applied waterproofing, after the concrete has been placed, can require specific cure times prior to application of a waterproofing system.
Select a System Within the Project’s Goal
After assessing the site conditions and construction process site, think about what will be required of the waterproofing system.
Here are some questions to ask:
- What level of protection is desired by the owner? Plan out how much time is needed. Different building types often require different solutions. Institutional structures, like hospitals, require a high level of protection and often utilize all the bells and whistles of a waterproofing system. Conversely, other structures might require a more streamlined approach to meet the budget requirements for the project. This may mean evaluating the difference between robust systems that utilize multiple waterproofing methods to create different levels of redundancy. Or it may mean selecting a single-sheet system that is more economical and easier to install. The critical thing to confirm is that you are selecting the right type of system for the project’s goals.
- Does your product have reliable features? Many high-performance waterproofing building materials have several features in common, so be sure to look for systems that differentiate themselves by offering:
• As few seams as possible
• Full adhesion to the substrate
• Layers of waterproofing membrane
• Efficient installation
- Does your product come with a warranty? Depending on the project and client, the importance of a warranty will vary. However, having a good product warranty in place allows for more peace of mind throughout every step of your project.
EPRO’s E.Assurance program is a No-Dollar-Limit warranty program offered by EPRO to give building owners superior warranty coverage in case of water ingress. EPRO offers a standard one-year warranty on all products and upgraded warranties for extended periods that cover material or material and labor.